Faced with the crisis, the automotive industry strengthens the resilience of its supply chains
Sachin Kamble, Professor of Supply Chain and member of the Anticipation, Innovation and Transformation Chair at EDHEC Business School, along with five other professors from leading business schools, discusses in an article originally published on The Conversation research to gain in-depth knowledge and measure the current impact of the pandemic on automotive supply chains.
The rapid and widespread spread of Covid-19 has created huge uncertainties in demand and disrupted global supply chains. More than 1.1 million direct jobs in the European Union's automotive sector have been affected since the start of the health crisis, according to ACEA (the European Automobile Manufacturers' Association).
The raging pandemic has challenged the aspirations of major automotive companies, and calls into question current supply chain resilience models.
Sachin Kamble, Professor of Supply Chain and member of the Anticipation, Innovation and Transformation Chair at EDHEC Business School, along with five other professors from leading business schools, conducted research to gain in-depth knowledge and measure the current impact of the pandemic on automotive supply chains.
The study is based on qualitative interviews with 88 automotive executives, and summarizes the different coping strategies employed by these companies and the lessons they are learning to build more resilient supply chains in the short and long term.
Short-term solutions
In the short term, the first strategy is to mitigate operational risks by relocating supply sources and using advanced industrial 4.0 technologies.
Supply logistics and manufacturing should be relocated within the same region to meet local demand and improve integration at all levels of the supply chain. In this way, the risk of disruption could be contained within the region, as there will be no threat of risk spillover from one region to another.
Indeed, one interviewee reveals that:
"One of our main weaknesses during the epidemic was the lack of real-time visibility across our entire supply chain. We are losing a great opportunity to support crucial business decisions...".
The second short-term strategy is to develop new skills in big data analysis and the use of real-time information systems.
These skills will provide real-time information on different levels of supply chain activity to overcome all the complex and uncertain challenges posed by Covid-19. Big data analytics can also improve supply chain forecasting capabilities, as demonstrated by the impressive support provided to several companies by improving information processing and simplifying the public procurement selection process.
One executive interviewed during the study points out:
"The data analysis we carried out told us that it would be better to keep factories running and build up stocks, absorbing fixed costs and preparing for the post-Covid-19 era".
Finally, companies in the industry are looking for better cooperation between supply chain players, to better prepare for future disruptions and help accelerate the use of digital technologies.
Indeed, most respondents stressed the importance of working together and sharing common goals and information in order to develop solid, coordinated strategies for faster recovery. It is very important to focus on humanitarian and social performance throughout the supply chain to mitigate the risk of disruption at all levels.
As one interviewee puts it:
"I think that before a disruption, we should have established strong relationships with key suppliers at all levels of the supply chain... we need to collaborate with everyone and share common goals".
Longer-term solutions needed
The study's testimonials also advise automotive companies to develop proactive and/or reactive long-term response strategies to speed up post-Covid recovery.
To manage immediate disruptions in a reactive way, the first step is to ensure security of supply and of the transport system. Interviewees thus stressed the urgent need for governments and companies to effectively coordinate the development of a long-term transport corridor with neighboring countries that will not be affected by such pandemics in the future.
Our discussions also showed that more effective use of emerging technologies is essential. This means ensuring the ability to use digital technologies to enable faster recovery from disruption and reduce the knock-on effect on the supply chain.
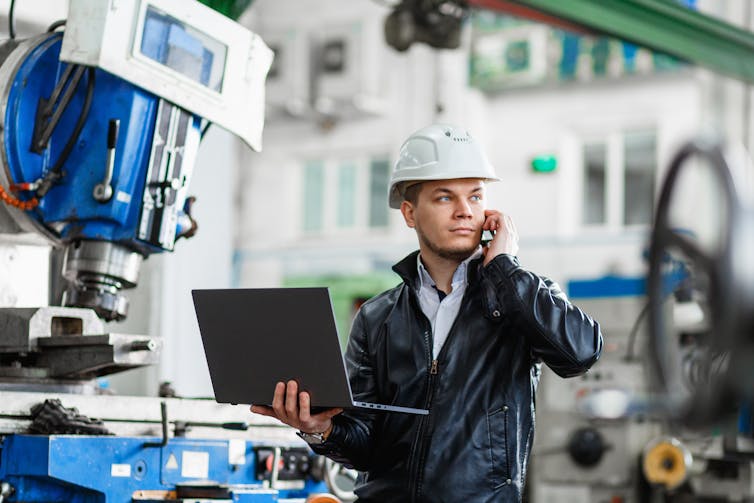
Still in the longer term, it emerged from our interviews that companies have an interest in adopting certain proactive strategies to prevent future situations of disruption.
These include, first and foremost, promoting digital transformation. This should enable manufacturing and service companies to develop resilience capabilities to better prepare for future disruptions in their supply chains.
The next step is to integrate risk management in an agile way. Indeed, the Covid-19 epidemic has highlighted the need to involve all supply chain stakeholders in creating an integrated approach to risk management in order to prevent disruptions and shocks from hitting their "invisible" suppliers upstream of the automaker's production line.
Finally, the need to develop corporate social responsibility (CSR) has never been greater. Adopting more holistic approaches, which merge both supply chain resilience and CSR practices, would indeed make it possible to better protect jobs and employees in the workplace. In particular, supply chain players in the automotive sector should learn from the disastrous social impact of the current pandemic, which has disrupted millions of lives worldwide, causing huge human and economic losses.
Our study also provides an insight into the airline industry. If you are interested, please feel free to read the full research report.
This article is republished from The Conversation under Creative Commons license. Read the original article.
Image by azerbaijan_stockers on Freepik